فرآیند تایید بخش تولید (PPAP) چیست؟
PPAP مخفف رایج در تولید است که مخفف عبارت Production Part Approval Process و به معنای فرآیند تایید بخش تولید است. به عنوان یک روش استاندارد که به طور گسترده استفاده می شود، مهم است که بفهمیم PPAP چیست و چرا اهمیت دارد. بیایید به یک PPAP نگاه کنیم و عناصر کلیدی این فرآیند را تجزیه کنیم.
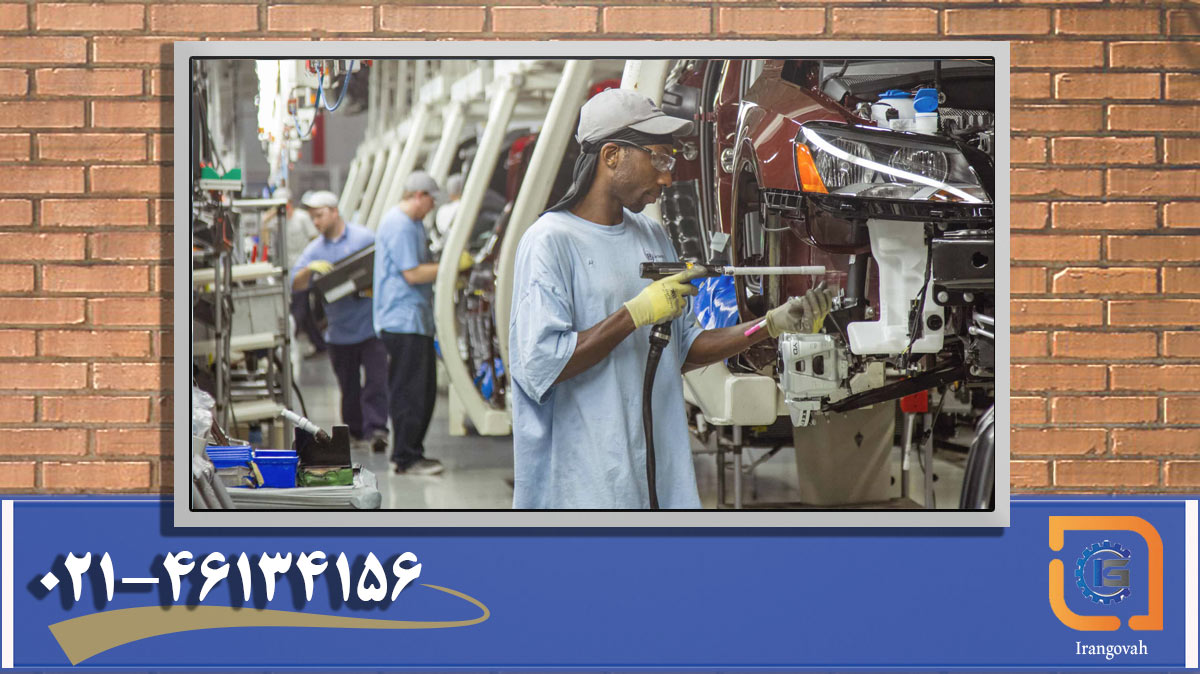
تعریف فرآیند تایید بخش تولید PPAP
فرآیند تأیید بخش تولید، یک رویه کلیدی در صنعت هوافضا و خودروسازی است تا اطمینان حاصل شود که قطعات تولید شده توسط تامین کنندگان به طور مداوم ایجاد می شوند. این یک فرآیند جامع است که از 18 مرحله تشکیل شده است که تضمین می کند هر قسمت انتظارات را برآورده می کند و هر بار با کیفیت بالا تولید می شود. در حالی که PPAP در هوافضا و خودرو سرچشمه می گیرد، به طور گسترده در سراسر تولید برای حمایت از فعالیت های کلیدی و تسهیل همکاری بین تامین کنندگان و مشتریان استفاده شده است.
این فرآیند همچنین بخشی از APQP (برنامه ریزی پیشرفته کیفیت محصول) است – به ویژه مرحله چهارم که مرحله اعتبار سنجی محصول و فرآیند است. دستورالعملهای کامل PPAP توسط گروه اقدام صنعت خودرو (AIAG) منتشر شده و میتوانید آن را خریداری کنید.
اهمیت PPAP
PPAP مهم است زیرا تضمین می کند که هر بخش ضروری که برای یک وسیله نقلیه یا ماشین آلات مورد نیاز است، هر بار با مشخصات صحیح ساخته می شود. دستورالعملهای واضحی را ارائه میکند تا تامینکنندگان دقیقاً بدانند که از آنها چه انتظاری میرود و روند ارتباطات را بهبود میبخشد.
برای تولید کننده، خروجی با کیفیت و اطمینان از برآورده شدن الزامات آنها در طول دوره تولید را امکان پذیر می کند. خطر اشتباه پیش رفتن و اجرای اقدامات اصلاحی را به حداقل می رساند و روند کلی را روان تر می کند.
فرآیند کامل PPAP
18 عنصر PPAP وجود دارد. همه اینها همیشه ضروری نیستند – به نیاز مشتری و پیچیدگی قطعه در حال ساخت بستگی دارد.
- مستندات طراحی – این شامل نقشههای فنی در کنار سفارش خرید میشود تا اطمینان حاصل شود که همه چیز مطابقت دارد و الزامات را برآورده میکند.
- اطلاعیه تغییر مهندسی – در صورتی که درخواست انجام اصلاحات در قسمت موجود باشد، این مورد وجود دارد.
- تأیید مشتری – باید مدرکی دال بر تأیید از بخش مهندسی مشتری وجود داشته باشد.
- حالت شکست طراحی و تجزیه و تحلیل اثرات (DFMEA) – یک ارزیابی ریسک جامع که تمام خرابی های احتمالی در طراحی را ترسیم می کند.
- نمودار جریان فرآیند – این نمودار تمام مراحل ایجاد قطعه را از ابتدا تا انتها نشان می دهد.
- حالت شکست فرآیند و تجزیه و تحلیل اثرات (PFMEA) – این به تمام شکست های احتمالی در خود فرآیند تولید نگاه می کند.
- طرح کنترل – اینها اقدامات پیشگیرانه ای هستند که برای کاهش احتمالات ذکر شده در PFMEA طراحی شده اند.
- تجزیه و تحلیل سیستم اندازه گیری – اینها مشخصات و جزئیات تمام تجهیزات مورد استفاده را ثبت می کنند.
- نتایج طرح بعدی – این یک بررسی اعتبار برای اطمینان از صحت اندازه گیری های روی نقشه در رابطه با نتیجه نهایی است.
- طرح و گزارش تأیید طراحی (DVP&R) – اینها سوابق تأیید اعتبار هر آزمایش انجام شده بر روی قطعه، شامل کلیه گواهینامه های مربوطه برای مواد هستند.
- کنترل فرآیند آماری – مستندسازی تمام فرآیندهایی که انجام خواهد شد و اجزایی که محصول را تشکیل می دهند.
- مستندات آزمایشگاهی واجد شرایط – این از گواهینامه های هر آزمایش آزمایشگاهی تشکیل شده است.
- بازرسی حذف ظاهری (ARI) – تأیید اینکه مشتری ظاهر محصول را تأیید کرده است.
- قطعات تولیدی نمونه – یک قطعه نمونه برای تایید مشتری در اختیار مشتری قرار می گیرد.
- نمونه اصلی – نمونه ای از نسخه نهایی محصول که نیاز به امضای مشتری دارد.
- کمک های چک کردن – لیستی از تمام بررسی های مورد نیاز که باید در طول تولید انجام شود، از جمله کالیبراسیون ابزار.
- الزامات خاص مشتری – این عنصر هر درخواست خاصی را که توسط مشتری ارائه می شود را در خود جای می دهد.
- فرم ضمانت ارسال بخش – این فرم خلاصه همه چیزهایی است که در امضاهای ارسال و اظهارنامه PPAP وجود دارد.
این یک لیست طولانی است، اما فرآیند PPAP تضمین می کند که همه چیز قبل و در حین تولید برنامه ریزی شده و در نظر گرفته شده است تا خطاها و ضایعات به حداقل برسد و محصولی با کیفیت بالا ارائه شود.