فرآیند بهبود مستمر چیست؟ – در 10 دقیقه مطالعه کنید
Continual improvement process فرآیند بهبود مستمر که در برخی مواقع CIP معرفی می شود، تلاشی مداوم برای بهبود محصولات، خدمات یا فرآیند سازمانی است.
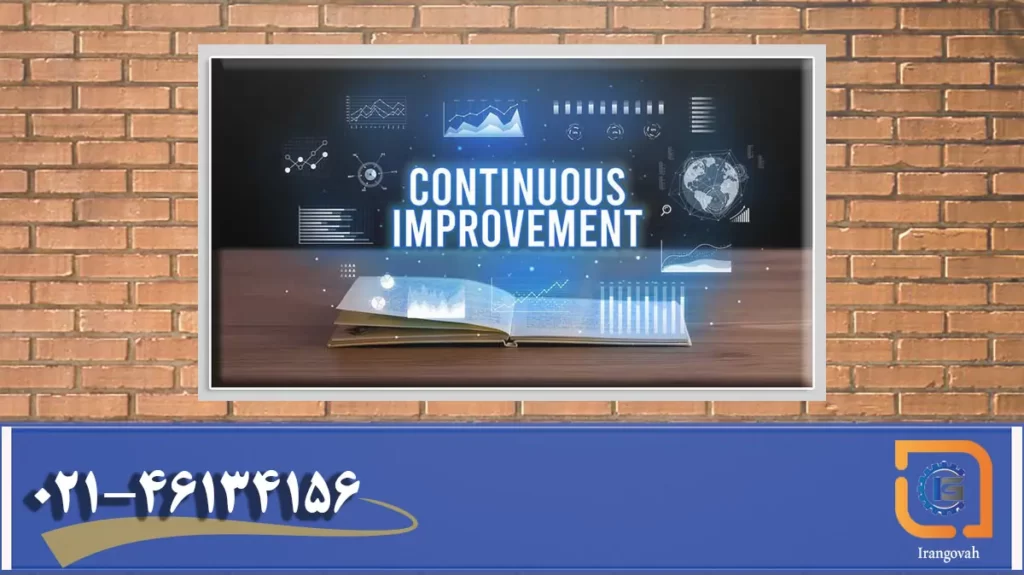
تعریف: بهبود مستمر عبارت است از تلاش مستمر برای بهبود فرآیند، محصول یا خدمات از طریق مراحل کوچک افزایشی.
فرآیند بهبود مستمر (CIP) یک تلاش مداوم برای بهبود محصولات، خدمات یا فرآیندها است. این یک رویکرد سیستماتیک شش مرحلهای برای برنامهریزی، ترتیب دادن و اجرای تلاشهای بهبود با استفاده از دادهها و جزئیات بیشتر در مورد چرخه شوهارت (Plan, Do, Study Act) است. CIP یک زبان و روش مشترک را ارائه می دهد که درک فرآیند بهبود را امکان پذیر می کند. CIP همیشه به اهداف و اولویت های هر سازمان مرتبط است.
- چرا باید از فرآیند بهبود مستمر (CIP) استفاده کنیم؟
- روش های بهبود مستمر چیست؟
- مراحل فرآیند بهبود مستمر چرخه شوهارت (CIP) چیست؟
- 6 مرحله فرآیند بهبود مستمر چیست؟
- چه زمانی باید اقدام به پیاده سازی فرآیند بهبود مستمر نماییم؟
- از چه روش هایی برای فرآیند بهبود مستمر استفاده می شود؟
- مزایای استفاده از ابزارهای بهبود مستمر چیست؟
- 14 ابزار فرآیند بهبود مستمر چیست؟
- چرا به فرآیند بهبود مستمر نیاز دارید؟
چرا باید از فرآیند بهبود مستمر (CIP) استفاده کنیم؟
اجرای یک فرآیند بهبود مستمر در یک سازمان باید در حال حاضر یک روش استاندارد باشد. مطالعات نشان داده اند که مزایای اصلی CIP (فرآیند بهبود مستمر) عبارتند از:
- افزایش بهره وری
- کار تیمی و روحیه بهتر
- چابکی بیشتر
- ضایعات کمتر
- کارایی بیشتر
- افزایش رضایت مشتری
- افزایش سود
روش های بهبود مستمر چیست؟
چند روش برای بهبود مستمر وجود دارد. چرخه شوهارت، شش سیگما، کانبان، تولید ناب، تئوری محدودیتها و مدیریت کیفیت جامع (TQM) تعدادی از این روشها هستند. هر روش به پرسنل برنامه کمک می کند تا محصولات، خدمات یا فرآیندها را با کاهش تغییرات، نقص ها و زمان چرخه بهبود ببخشند.
مراحل فرآیند بهبود مستمر چرخه شوهارت (CIP) چیست؟
چرخه شوهارت معروف به چره بهبود مستمر برای درک چرخه عمر پروژه و برنامه محوری است. چهار مرحله مرتبط با CIP با استفاده از چرخه شوهارت وجود دارد:
- فاز 1 “طرح”: برای تغییر برنامه ریزی کنید و فرصت های بهبود را شناسایی کنید.
- فاز 2 “انجام”: تغییرات شناسایی شده را اجرا کنید.
- فاز 3 “مطالعه”: بررسی کنید تا مشخص شود آیا تغییر نتیجه مطلوبی داشته است یا خیر.
- فاز 4 “عمل”: در صورت موفقیت، آن را در سراسر سازمان و فرآیند اجرا کنید.
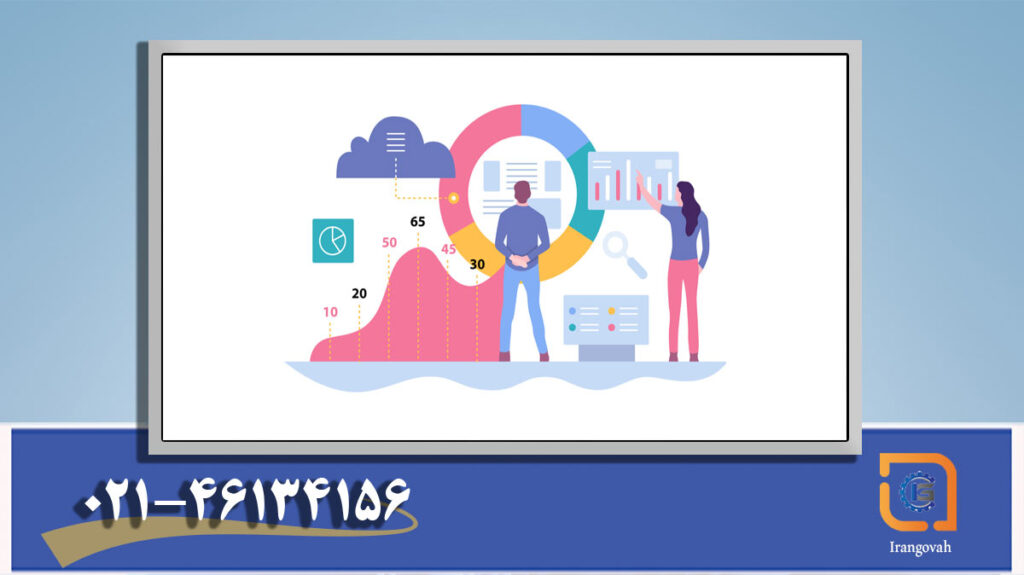
6 مرحله فرآیند بهبود مستمر چیست؟
اکثر متدهای CIP (فرآیند بهبود مستمر) از شش مرحله اساسی زیر در اجرای خود پیروی می کنند.
- مرحله 1: شناسایی فرصت بهبود: فرآیند مناسب را برای بهبود انتخاب کنید.
- فرآیند ارزیابی
- چالش/مشکل را انتخاب کنید
- مرحله 2: تجزیه و تحلیل: شناسایی و تأیید علت(های) ریشه ای.
- مرحله 3: اقدام: اقداماتی را برنامه ریزی و اجرا کنید که علت(های) اصلی را اصلاح می کند.
- مرحله 4: نتایج مطالعه: اقدامات انجام شده برای دستیابی به هدف را تأیید کنید.
- مرحله 5: استاندارد کردن راه حل: اطمینان حاصل کنید که سطح بهبود یافته عملکرد حفظ می شود.
- مرحله 6: برای آینده برنامه ریزی کنید:
- برنامه ریزی کنید که با مشکلات باقی مانده چه کاری باید انجام شود
- ارزیابی اثربخشی تیم
- هدفی را برای بهبود تعیین کنید
چه زمانی باید اقدام به پیاده سازی فرآیند بهبود مستمر نماییم؟
زمان خاصی برای شروع استفاده از فرآیند بهبود مستمر ” Continuous improvement process” وجود ندارد، اما هر چه زودتر، بهتر است. در زیر لیستی از زمان هایی است که من معتقدم CIP باید اجرا شود:
- آغاز یک پروژه جدید
- توسعه فرآیندها و رویه ها
- توسعه یک محصول یا خدمات جدید یا بهبود یافته
- برنامه ریزی جمع آوری و تجزیه و تحلیل داده ها
- اجرای هرگونه تغییر در یک فرآیند
- هر زمان که شکستی رخ دهد
از چه روش هایی برای فرآیند بهبود مستمر استفاده می شود؟
- محک زدن
- تجزیه و تحلیل میدان نیرو
- فلوچارت ها
- نمودار میل
- تکنیک دلفی
- نمودار پارتو
- نمودار علت و معلول
- نمودار پراکندگی
- برگه را بررسی کنید
- نمودار کنترلی
- شاخص و نسبت قابلیت فرآیند
- ISO 14001
مزایای استفاده از ابزارهای بهبود مستمر چیست؟
تولیدکنندهای که مسیر بهبود مستمر را آغاز کرده است، ابزارها و تکنیکهای زیادی برای انتخاب دارد. این ابزارها در طول سالها طراحی شدهاند تا با شناسایی ناکارآمدیها در فرآیندهایشان و یافتن راههایی برای بهبود آنها، به سازمانها در تلاش برای کارایی عملیاتی کمک کنند.
در عصر دیجیتال امروزی که نیازمند نوآوری و چابکی است، ابزارهای فرآیند بهبود مستمر (CIP) فرآیند بسیار مرتبط باقی میمانند – و با فناوریهایی مانند تحلیل پیشبینیکننده، چاپ سهبعدی و داشبورد دیجیتال تقویت میشوند. زمانی که سازمانهای تولیدی از ابزارهای بهبود مستمر و فناوریهای مدرن استفاده میکنند، مسائل احتمالی تولید را میتوان خیلی سریعتر شناسایی کرد.
در حالی که ابزارهای بهبود مستمر پایه و اساس بهترین تکنیکها و ساختار را ایجاد میکنند، فنآوری دید در زمان واقعی، مسئولیتپذیری بیشتر، ردیابی بهتر و بسیاری موارد دیگر را برای فرآیند بهبود به ارمغان میآورد. بنابراین مهم است که بدانید از کدام ابزار – و چه زمانی استفاده کنید. در اینجا برخی از محبوبترین ابزارهای بهبود مستمر و نحوه سودمندی آنها برای عملیات مدرن آورده شده است.
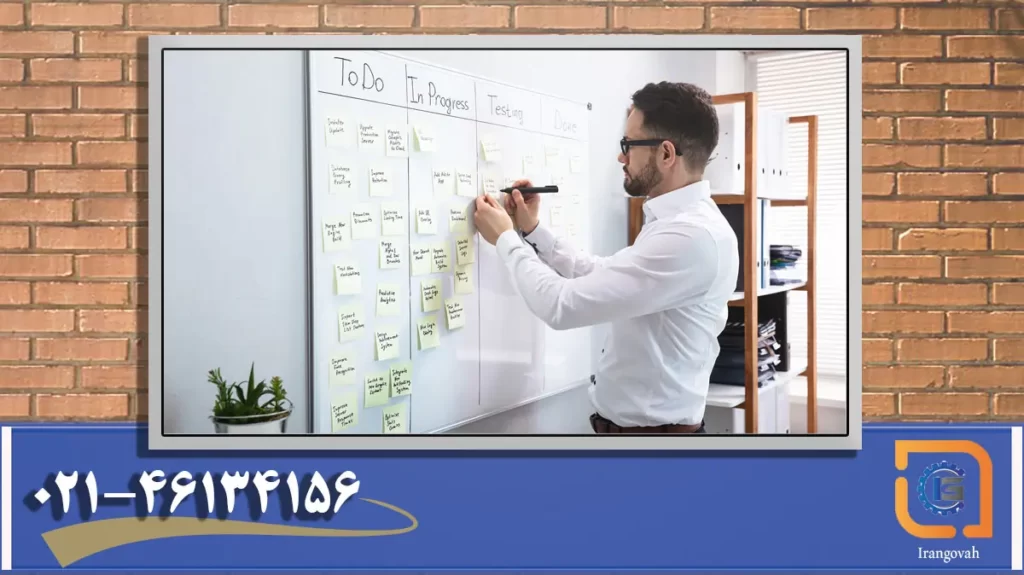
14 ابزار فرآیند بهبود مستمر چیست؟
1. کایزن (Kaizen)
کایزن یک اصطلاح ژاپنی به معنای “تغییر به سوی بهتر” یا “بهبود مستمر” است. هدف آن بهبود فرآیندها، بهره وری و سود از طریق حذف ضایعات است. این می تواند تقریباً برای هر فرآیند یا فعالیتی در تجارت اعمال شود یا توسط افراد برای بهبود جنبه های خاصی از زندگی خود استفاده شود.
در محل کار، یک استراتژی کایزن فرهنگ سازمانی بهبودهای تدریجی در مقیاس کوچک را القا می کند که در آن همه در بهبود محصولات، فرآیندها و خودشان برای نتایج بهتر در طول زمان مشارکت می کنند. این فرهنگ برای تولیدکنندگانی که از فناوریهای دیجیتال استفاده میکنند، کلیدی است تا کارمندان به تحول دیجیتال بپردازند.
2. گمبا (Gamba)
Gemba یک اصطلاح ژاپنی است که مستقیماً به عنوان “مکان واقعی” ترجمه شده است. در حلقههای بهبود، gemba مکانی است که در آن ارزش واقعی ایجاد میشود. در تولید، جمبا کف کارخانه ای است که در آن محصول تولید می شود.
“رویکرد gemba” یک تکنیک مدیریت و حل مسئله بسیار موثر است که محل کار واقعی را به عنوان مرکز جمع آوری داده ها دارد. «گمبا پیاده روی» شامل راه رفتن مدیریت و مشاهده آنچه در حال رخ دادن است، تعامل با کارگران خط مقدم و جستجوی فرصت های بهبود است. پیاده سازی Gemba از یک فرآیند و پروتکل واضح پیروی می کند تا از اثربخشی آنها اطمینان حاصل شود تا هر مشکلی به موقع حل شود.
3. کار استاندارد (Standard work)
کار استاندارد یک اصل اساسی در تولید ناب است. این یک فرآیند رسمی تعریف شده و مستند برای تولید دقیقاً همانطور که طراحی شده، است. این شامل توالی و نرخ تولید برای برآوردن تقاضاها، استانداردسازی مواد و قطعات در حال فرآیند، و به حداقل رساندن نگهداری موجودی برای بهینه سازی عملیات است.
قابل پیش بینی بودن کار استاندارد تغییرات را کاهش می دهد و امکان انجام روتین را فراهم می کند. این به کارگران امکان می دهد تا محصولات قابل تحویل خود را درک کنند، پیشرفت را دنبال کنند و ایمن کار کنند و می تواند به حذف ضایعات و فعالیت های ناکارآمد کمک کند.
اما کار استاندارد برای تمام سطوح کارگران و رهبران اعمال می شود. در حالت ایدهآل، فقط گردش کار سطح پایین استاندارد شده است تا انعطافپذیری و خلاقیت سطح بالاتر را امکانپذیر سازد. این تضمین می کند که فرآیند استانداردسازی به جای محدود کردن، آزاد کننده است. استانداردها باید مرتباً بازنگری و بازتعریف شوند تا با چابکی و نوآوری مورد نیاز یک سیستم تولید مدرن مطابقت داشته باشند.
4. استاندارد 5S
استاندارد 5S یک روش سازماندهی محل کار است که هدف آن برقراری اصول انضباط، نظم، تمیزی، مالکیت، مسئولیت و غرور است. کارایی را به حداکثر می رساند و در عین حال محیط کاری ایمن را تضمین می کند. این یک شالوده اساسی ایجاد می کند که همه بهترین شیوه های دیگر می توانند بر اساس آن پیشرفت کنند و می تواند تأثیر مثبتی بر نتیجه سازمان داشته باشد.
پنج مفهوم ژاپنی زیر 5S را تشکیل می دهند:
- مرتب و واضح
- بدرخشید
- به ترتیب تنظیم کنید
- استاندارد کردن
- حفظ کنید
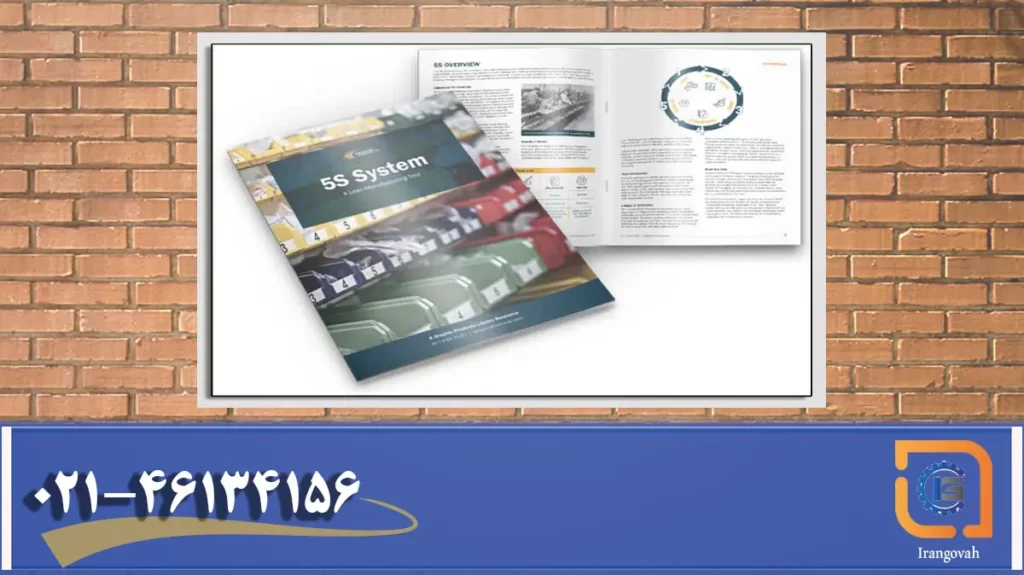
5. تجزیه و تحلیل تلفات و ضایعات
فعالیتهای بیهوده، روشها و فرآیندهای بیارزشافزودنی هستند که باعث رکود رشد میشوند و حذف آنها یک اصل اساسی در روششناسی ناب است. تجزیه و تحلیل زباله شامل شناسایی، کمی کردن، حذف و جلوگیری از زباله در محیطی مانند تولید است. Taiichi Ohno که یکی از بنیانگذاران سیستم تولید تویوتا (TPS) به حساب می آید، هفت زباله ذکر شده در زیر را توسعه داد:
- حمل و نقل: جابجایی و انتقال غیر ضروری مواد
- موجودی: مواد اولیه بیش از حد، WIP یا کالاهای نهایی
- حرکت: هر حرکت تجهیزات یا کارمندی که ارزش افزوده ندارد
- انتظار (یا تأخیر): هر کارمند یا تجهیزاتی که در دسترس است اما منتظر نوعی ورودی است
- تولید بیش از حد: تولید بیش از آنچه مشتری نیاز دارد
- پردازش: استفاده از ظرفیت یا انرژی بیش از حد بدون ارزش افزوده
- تصحیح: محصول معیوب نیاز به کار مجدد دارد
6. DMAIC
DMAIC یک تکنیک پنج مرحله ای چرخه ای و ساختار یافته (تعریف، اندازه گیری، تجزیه و تحلیل، بهبود، کنترل) است که برای بهبود فرآیند جاری زمانی که مشکل پیچیده است یا خطرات زیاد است، استفاده می شود. DMAIC اغلب برای هدایت پروژه های شش سیگما استفاده می شود، اما به شش سیگما محدود نمی شود.
پنج مرحله به ترتیب انجام می شود:
- همه آنچه را که در مورد مشتری هدف، جریان فرآیند، اهداف پروژه و اهداف می دانیم تعریف کنید
- وضعیت فعلی عملکرد فرآیند تجاری مورد تجزیه و تحلیل را اندازه گیری کنید
- عملکرد فعلی را تجزیه و تحلیل کنید و با شناسایی تفاوت بین عملکرد فعلی و هدف، مشکل را جدا کنید
- با استفاده از طرح های بهبودی که در این مرحله طوفان مغزی و مستند شده است، فرآیند را بهبود بخشید
- تلاش بهبود را کنترل کنید تا اطمینان حاصل شود که پایدار است، برای مثال از طریق کار استاندارد رهبر
7. PDCA
یکی از ابزارهای کلیدی بهبود مستمر در تولید، چرخه PDCA یک روش علمی ساختاریافته را برای نهادینه کردن فرآیند بهبود مستمر در سراسر یک سازمان از طریق یک رویکرد چهار مرحله ای ارائه می دهد: برنامه ریزی، انجام، بررسی، عمل کنید.
چرخه PDCA به شرح زیر است:
- برنامه ریزی: اهداف سازمانی خود و نحوه دستیابی و اندازه گیری آنها را ترسیم کنید
- انجام دهید: برنامه را اجرا کنید و مشاهده کنید و درک کنید که چگونه به محیط کار واقعی ترجمه می شود
- بررسی: اندازه گیری تأثیر طرح در برابر معیارهای تعیین شده در مرحله اول چرخه PDCA
- اقدام: هرگونه تعدیل یا اصلاح مورد نیاز در برنامه را برای بهینه سازی نحوه تحقق بهترین اهداف استراتژیک خود انجام دهید
8. A3
گزارش حل مسئله A3 یک ابزار جامع و ساختار یافته حل مسئله است که برای تجزیه و تحلیل علت ریشه ای استفاده می شود تا از تکرار مشکلات پیچیده جلوگیری کند. مشکل می تواند از سطح استراتژیک گرفته تا یک مشکل فردی با یک محصول یا فرآیند متفاوت باشد.
این گزارش به یک صفحه A3 محدود شده است و پرسش و گفتگوی دقیق بین مالک A3 و مشارکت کنندگان کلیدی را تشویق می کند. اطلاعات ضروری به طور مختصر و توصیفی و اغلب با استفاده از نمودارها جمع آوری می شود. بخشهای مختلف یک دید پرنده از کل پروژه بهبود ارائه میدهند و راهنمایی در مورد چگونگی حل مشکل ارائه میدهند. داشبوردهای دیجیتال به قابل مشاهده کردن گزارش A3 برای همه ذینفعان آسیب دیده کمک می کنند.
9. 5 چرا
5چرا یک ابزار اساسی برای حل مسئله است. با پرسیدن “چرا” بارها و بارها، علت اصلی یک مشکل آشکار می شود. پنج (یا کمتر) تکرار پرسیدن «چرا» به طور کلی برای رسیدن به علت اصلی کافی است. استفاده از اصول تفکر انتقادی برای حذف مفروضات نامربوط و تله های منطقی مهم است. شرکت تویوتا موتور با موفقیت از این روش برای حل مشکلات تولید استفاده کرده است.
10. نمودار استخوان ماهی
نمودار استخوان ماهی، یا نمودار ایشیکاوا، نمایشی گرافیکی از عواملی است که بر نتایج تأثیر می گذارند و برای یافتن علت اصلی یک مشکل یا نقص استفاده می شود. روابط علت و معلولی در دستههای مختلف افراد، روشها، تجهیزات، محیط، مواد و اندازهگیری تحلیل میشوند. نمودار استخوان ماهی اغلب در طراحی محصول و فرآیند استفاده می شود و همچنین می تواند برای شناسایی فرصت ها برای بهبود بیشتر فرآیند استفاده شود.
11. کانبان
کانبان از سیستم تولید تویوتا به عنوان یک سیستم زمانبندی برای تولید در زمان (JIT) سرچشمه گرفته است. این یک اصطلاح ژاپنی است، “کان” به معنای “بصری” و “بان” به معنای “کارت”. کانبان نشانگرهایی هستند (بعضی اوقات، اما نه همیشه، کارت های بصری) که نشان می دهد باید اقدامی انجام شود. «عمل» میتواند وظیفهای باشد که باید انجام شود، یا انبار یا قطعاتی که باید سفارش داده شوند. بسیار مهم است که مردم به نشانه های بصری به سرعت پاسخ دهند.
با استفاده از فناوری، تابلوهای Kanban بسیار تعاملی تر می شوند، یک نمای کلی در زمان واقعی ارائه می دهند و فوراً گلوگاه های سیستم را نشان می دهند. داده ها را می توان برای تولید گزارش عملکرد و برنامه اقدام بهبود بعدی صادر کرد.
12. مدیریت بصری
مدیریت بصری به صورت بصری اطلاعات کلیدی را با استفاده از نمایشگرهای اطلاعات دیجیتالی، کنترلهای بصری، برچسبها، علائم و کدگذاری رنگی، به اشتراک میگذارد. این امکان اندازه گیری و کنترل موثر عملکرد را فراهم می کند و بهترین روش برای شناسایی شاخص های کلیدی، توافق بر سر اهداف و ارائه بازخورد بصری و دوره کوتاه در مورد عملکرد در برابر این اهداف است.
در تولید مدرن، داده های بلادرنگ به صورت بصری بر روی داشبورد دیجیتال نمایش داده می شوند. این با ارائه اطلاعات بلادرنگ که به راحتی برای همه ذینفعان قابل دسترسی است، بسیار ارزشمند می شود. تیم ها همچنین می توانند به سرعت در موقعیت های کنترل و خارج از کنترل شناسایی شوند.
مدیریت بصری مالکیت و مسئولیت پذیری را ارتقا می دهد. همراه با کار استاندارد و مسئولیت پذیری روزانه، مدیریت بصری سه پایه ای را تشکیل می دهد که سیستم های مدیریت ناب موثر بر روی آن ساخته می شوند.

13. نقشه فرآیند
یک نقشه فرآیند یا نمودار جریان بینشی را در مورد یک فرآیند می دهد زیرا به صورت بصری جریان کل فرآیند یا زیرفرایند را توصیف می کند. می توان آن را روی کاغذ یا با استفاده از نرم افزار انجام داد و فعالیت ها و افراد یا بخش های مسئول هر فعالیت را مستند می کند.
نقشه های فرآیند نشان می دهد که چگونه یک فرآیند انجام می شود، اما می توان از آنها به عنوان یک ابزار بهبود نیز استفاده کرد. تیمها پس از ترسیم فرآیند، آن را تجزیه و تحلیل میکنند، که اغلب نشان میدهد که در کجا فرآیند باید بهبود یابد.
14. نقشه برداری جریان ارزش
نقشه جریان ارزش یک نمایش بصری (امروزه اغلب در قالب دیجیتال) از جریان اطلاعات و/یا مواد و فعالیت ها از ابتدا تا انتهای جریان ارزش سازمان است. نگاشت جریان ارزش (VSM) حاوی اطلاعات بیشتری در رابطه با جریان (پارامترهای جریان)، مانند زمان هدایت فرآیند و چرخه، نسبت ارزش افزوده، نسبت کیفیت و بازده گذر اول، نسبت به نقشههای فرآیند معمولی است.
VSM ابزار مفیدی برای ثبت وضعیت فعلی و هدف یک فرآیند است. می توان از سطح فرآیند ماکرو تا خرد استفاده کرد.
چرا به فرآیند بهبود مستمر نیاز دارید؟
نیاز به رویکرد یکپارچه، به دست آوردن مزایای کامل ابتکارات بهبود مستمر در کارخانههای مدرن مستلزم یک رویکرد ساختاریافته و یکپارچه است.
ابتکارات بهبود باید در کل عملکردها، افراد، فرآیندها و سیستمهای سازمان همسو شود تا در نهایت راهحلی جامعتر و پایدار ارائه شود. به این ترتیب، بهبود مستمر (1) به فرهنگ سازمان تبدیل می شود که در آن همه اعضای تیم – نه تنها مدیریت – مسئولیت بهبودها و راه حل های بالقوه را بر عهده می گیرند.
یک سیستم مدیریت بهبود مستمر دیجیتال به سازمان ها کمک می کند تا با ارائه این رویکرد ساختاریافته و یکپارچه برای بهبود مستمر، به نتایج پایدار دست یابند. سیستم مدیریت صحیح همچنین به تولیدکنندگان کمک می کند تا با رویدادهای مخرب، افزایش رقابت، بهبود رضایت مشتری در میان تقاضاهای مصرف کننده در حال تغییر و تحول دیجیتال کنار بیایند.
پرسش های متداول
فرآیند بهبود مستمر چیست؟
فرآیند بهبود مستمر (CIP) یک تلاش مداوم برای بهبود محصولات، خدمات یا فرآیندها است. این یک رویکرد سیستماتیک شش مرحلهای برای برنامهریزی، ترتیب دادن و اجرای تلاشهای بهبود با استفاده از دادهها و جزئیات بیشتر در مورد چرخه شوهارت (Plan, Do, Study Act) است. CIP یک زبان و روش مشترک را ارائه می دهد که درک فرآیند بهبود را امکان پذیر می کند. CIP همیشه به اهداف و اولویت های هر سازمان مرتبط است.
روش های بهبود مستمر چیست؟
چند روش برای بهبود مستمر وجود دارد. چرخه شوهارت، شش سیگما، کانبان، تولید ناب، تئوری محدودیتها و مدیریت کیفیت جامع (TQM) تعدادی از این روشها هستند. هر روش به پرسنل برنامه کمک می کند تا محصولات، خدمات یا فرآیندها را با کاهش تغییرات، نقص ها و زمان چرخه بهبود ببخشند.
14 ابزار فرآیند بهبود مستمر چیست؟
1. کایزن (Kaizen)
2. گمبا (Gamba)
3. کار استاندارد (Standard work)
4. استاندارد 5S
5. تجزیه و تحلیل تلفات و ضایعات
6. DMAIC
7. PDCA
8. A3
9. 5 چرا
10. نمودار استخوان ماهی
11. کانبان
12. مدیریت بصری
13. نقشه فرآیند، و
14. نقشه برداری جریان ارزش